Today I needed to work on a lasercut project for the Camp Mustang that will be happening next week at the high school. Camp Mustang is a 2 day in school event for elementary and secondary school students within the Medford school district. I will be offering students CAD lessons, lasercutting, and some basic electronics. Several years ago, at my previous teaching job, I created a lasercut bug that could be assembled and then an LED and battery press fit into it so it lit up. I’ve created something similar for students but more of a robot shape. I’m still waiting on some material to cut each one out on, hoping that arrives today – otherwise I will be rushing around next week to get these cut for the students to assemble. For now, you can see the image that is used to lasercut on our Epilog Fusion Pro lasercutter.
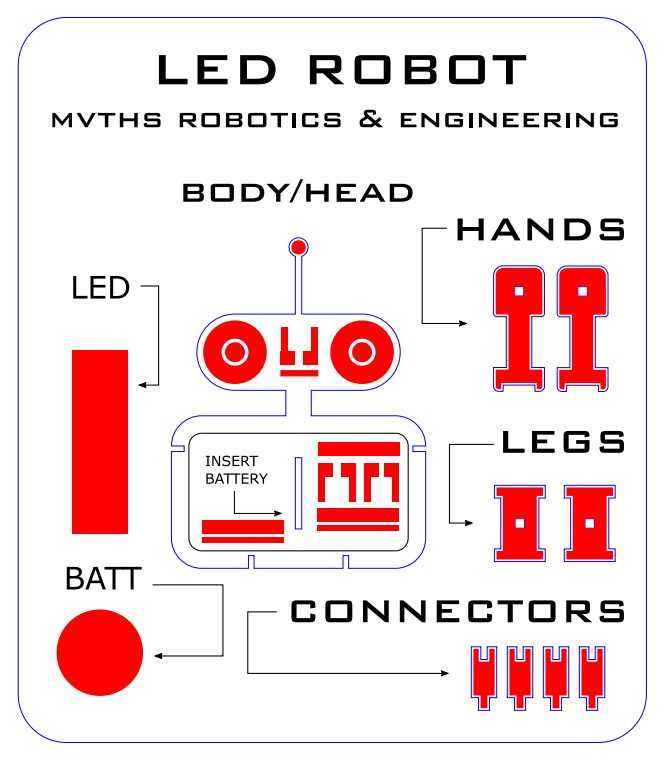